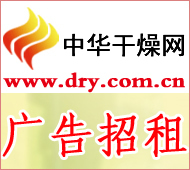
In recent years, lithium-ion battery-related policies have been successively introduced to promote the establishment of upstream and downstream industries. The beautiful market prospects have attracted various industrial capitals. However, under the influence of factors such as low-end homogenization competition and technical security risks, the industry is facing a large-scale application dilemma.
In response to this situation, the 2012 Beijing Power Lithium-ion Battery Technology and Industrial Development International Forum was held recently. Professor Wu Feng, Director of the National High-tech Green Materials Development Center and Vice Chairman of the China Battery Industry Association believes that the lithium battery industry's extensive expansion The path weakens the technological innovation of key materials. If China wants to take a place in the fierce international game, it must work hard at the source and accelerate the design and layout of key materials.
Through field research, it has been found that the diaphragm industry, which is a key component of lithium batteries and the most valuable for investment, is showing a great leap forward. However, the quality positioning is still concentrated in the low-end and high-quality diaphragms that meet market demands are still a blue ocean.
Low-end invalid supply surplus
The main constituent materials of the lithium battery include a positive electrode, a negative electrode, an electrolyte, and a separator. The diaphragm is the most critical inner component and core material of the lithium battery.
As the lithium battery capacity, cycle capacity and charge and discharge current density and other key performance are directly related to the diaphragm, coupled with the technical barriers to the production of high diaphragm, the potential investment value for the diaphragm industry for many domestic manufacturers to compete.
According to Feng Zhiqiang, general manager of Hebei Jinli New Energy Co., in addition to technical barriers and application value, the high gross profit margin of the diaphragm is the most realistic factor in attracting companies to enter this field. The cost of the diaphragm accounts for about 30% of the cost of the entire lithium battery, but the gross profit rate can reach more than 60%. The gross profit rate is the highest among the four lithium battery materials.
The huge business opportunities have enabled the domestic lithium battery separator industry to rise rapidly and a large number of diaphragm manufacturers have emerged within a short time.
According to incomplete statistics, currently there are nearly 50 companies in China that are currently constructing and planning to invest in lithium battery separator projects. The estimated new production capacity exceeds 600 million square meters. In terms of the industry as a whole, of the nearly 50 companies involved in the lithium battery separator business, fewer than 20 have established production lines, and most of the remaining half are in the construction and proposed phases. Among them, there are 8 listed companies in the Shangma diaphragm project: Southeast China, Zhuozhou Mingzhu, Fosu Technology, Yuntianhua, Jiujiu, Shenzhen Huicheng, Nanyang Science and Technology, and Fluorine.
Among the 8 listed companies, Chuzhou Pearl has completed 3 million square meters of single-cell Lithium battery separator experimental production line at the end of 2011, and began to supply bulk quantities to Suzhou Xingheng and other downstream lithium battery companies; Yuntianhua Subsidiary Chongqing Nuomi Technology The annual output of 15 million square meters of wet lithium-ion battery diaphragm production line was put into operation in October 2011; Fosuy Technology Subsidiary Jinhui High-tech Co., Ltd. is one of the earliest companies to realize wet process industrialization in China, and has now achieved an annual output of 2500 Million square meters of production capacity.
It is noteworthy that many domestic companies have entered the diaphragm area to develop the lithium battery industry at the same time, which has brought two major problems. On the one hand, the total planned production capacity has far exceeded actual shipments. On the other hand, these actual shipments can be accepted by the market. The proportion is less than 30%.
"If there is no reliable source of technology and continuous research and development capabilities, the low-end repeated construction and price competition will inevitably affect the healthy development of the diaphragm industry," said a person from CITIC Guoan Subsidiary League Solid Power Technology Co., Ltd.
Zheng Qing, an analyst at Orient Securities, pointed out in a research report that in 2011, China's production capacity of diaphragm manufacturers with actual output capacity was only 31 million square meters, far lower than domestic domestic production capacity. The reason for this is that in addition to the possible difference between the planned production capacity and the actual production capacity, the invalid supply caused by the disconnection between the structure of the company's designed production capacity and the market demand is worthy of caution.
In this regard, Feng Zhiqiang believes that the domestic diaphragm production capacity is not more than but can not meet market demand, many diaphragm companies have low technological content, simply can not break into the high-end market, enter the world's mainstream battery manufacturers supply system. With the increase of pure production capacity but the quality of the enterprise cannot meet the demand of the mid-to-high end market, the low price homogenous competition will surely cause the industry to reshuffle. The short-term emergence of lithium battery separators has caused a large number of companies to have more worries than joy.
Wu Dayong, deputy chief of Beijing First Spray Technology Development Co., Ltd. and researcher of the Institute of Physics and Chemistry of the Chinese Academy of Sciences, said that the lithium battery separator project is not simply a film stretch, but an industry with high technological content and advanced technology. Sex, equipment, management level, production process control, cost control, and skill level of skilled workers all put forward high requirements.
"In the large-scale production of diaphragms, technical difficulties are not only manifested in the uniform pore formation, the control of the thickness uniformity, the consistency of the material strain, but also the heat resistance of the separator and the electrophilicity of the electrolyte. Sexuality.†Wu Dayong thinks.
Composite diaphragm application is the trend
In the four material systems of lithium batteries, the diaphragm materials have already achieved initial mass production, but the vast majority are low-end consumer electronics applications. Due to the large gap between domestic companies' production technology, product performance and R&D system and international advanced level, high-quality battery separators are almost blank in China.
According to Yuan Xiangyun, head of Guotai Huarong Chemical New Material Co., Ltd., a subsidiary of Jiangsu Guotai Holding Co., Ltd., at present, domestic lithium battery separator products have partially replaced imported products in the traditional consumer electronics field, but the composite separator in lithium battery is basically It is still imported.
“It can be seen from this that lithium-ion battery diaphragm localization substitution is the expectation of the lithium battery industry. The premise is that we must understand the technical requirements of the upstream lithium battery customers, the performance requirements of the battery separator materials, the process requirements of the battery separator, and Other battery materials match the electrochemical performance and safety requirements, said Wu Feng.
Although China's lithium battery separator mainly consumes consumer electronics products, under the background that the power battery industry is strongly supported by national policies, the demand for vehicle lithium battery separator materials in China will increase significantly in the future. More stringent requirements.
A number of industry experts interviewed said that the current domestic lithium battery separators are mainly dry-processed PP and wet-processed PE, mostly low-end quality. At this stage, certain technologies are applied to the surface of the separator. It is possible to satisfy the application of vehicle power battery by improving the liquid absorption performance and heat resistance.
Taking the ultra-high molecular weight polyethylene wet diaphragm manufactured by Hebei Jinli New Energy Company as an example, the R&D team of the company has been devoting itself to the research and development of high-end diaphragms. Mass production was realized in May 2002. Currently, there are more than 30 lithium batteries in the middle-to-high end of the country. The company launched a technology and product cooperation.
Rong Qiang, chief engineer of Hebei Jinli New Energy Co., Ltd. deeply understands: “The advantages and disadvantages of lithium battery separators directly affect the characteristics of the battery's capacity, circulation, and safety performance. Jinli New Energy is the first to introduce the most advanced lithium battery separator production technology in Japan. The results of the expert review of the industrialized companies show that the ultra-high molecular weight polyethylene wet diaphragm we produced has reached the quality of diaphragms of similar companies in Japan.â€
In fact, in order to further improve the safety performance of lithium batteries, Hebei Jinli New Energy Co., Ltd. has also cooperated with the Chinese Academy of Sciences to successfully develop a high-temperature resistant diaphragm coating slurry. The separator using this slurry can effectively improve the heat resistance of the power battery under high magnification. Improve the safety performance of the power battery. “At the same time, in order to further improve the ultra-high rate discharge performance of lithium batteries and meet the special needs of military batteries, the company has reached a cooperation R&D intention with the Military Chemical Power Supply and Development Center of the General Armament Department and has formed a complete basic R&D system.†Feng Zhiqiang Told reporters.
Le Jun, a researcher at the Shanghai Institute of Ceramics, Chinese Academy of Sciences and deputy director of the special laboratory for inorganic coatings, believes that the coating modification process innovation is only the first level of development of the diaphragm industry. The development and application of the new composite diaphragm system is the next-generation vehicle. The dominant technology route with power batteries.
According to Cui Guanglei, a researcher at the Qingdao Institute of Bioenergy and Process, who has long been engaged in the research of energy storage battery materials in the field of new energy, it is difficult for the existing diaphragm materials to meet many standards and requirements in terms of comprehensive performance. Therefore, there is an urgent need to develop new composite films. And electrolyte materials to meet the performance of the battery separator and electrolyte at the same time, using a variety of materials composite or synthesis of new polymer single ion conductor to prepare composite film, can further improve the battery's high melting point and safety.
For the development trend of the diaphragm, Zhang Liangyong, an analyst in the electronic industry of China Merchants Securities, believes that two technical routes are required. One is the development of consumer lithium battery diaphragm technology that is more lean, mainly for distributed application architectures such as mobile phones and notebooks. Improve the capacity and portability of lithium batteries; the other is the development of power battery diaphragms that tend to use thick film or multi-layer composite diaphragms, mainly for large-scale power applications such as electric vehicles and large-scale energy storage power stations.
Certificate |
ISO14001, ISO18000, ISO9001 Certificate,
and GS certificate from TUV Company of Germany.
|
Color | Various, according to your requirements |
Materials |
A. Plastic parts: Imported LLDPE E. Outer cover: Soft Covering PVC
(Different material is available according to your needs)
|
Advantage |
a.Anti-UV
b.Anti-static
c.Security
d.Environmental protection e.Uneasy to lose shape |
Function |
1.Can protect children safe when they playing indoor, and let they enjoy the play freely 2.Suitable for improving Children energy and imagination 3.Helping them grow up happily, cleverly, and healthily |
Age Range | Children |
Apply to | Amusement park, gymnasium, Kindergarten, Preschool, etc. |
Packing | Standard export packing |
Remark |
We can design and produce as your requirements |
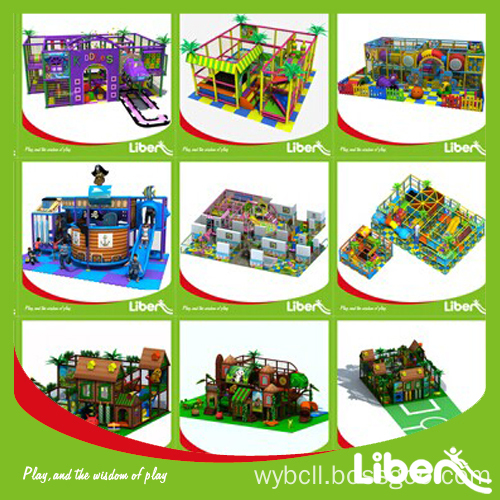
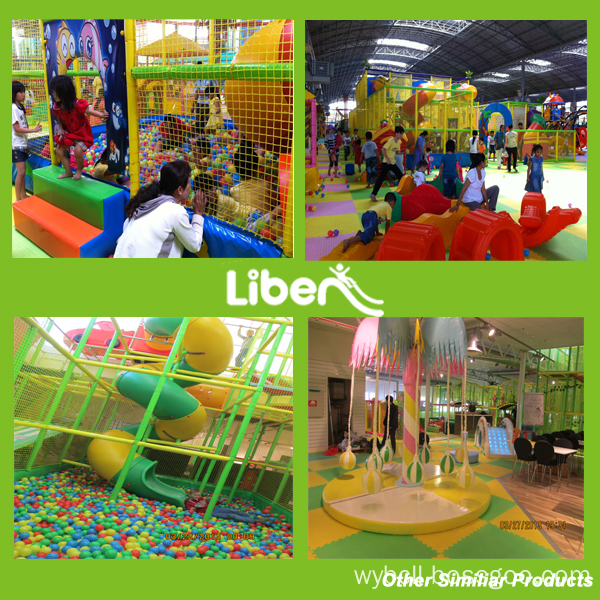
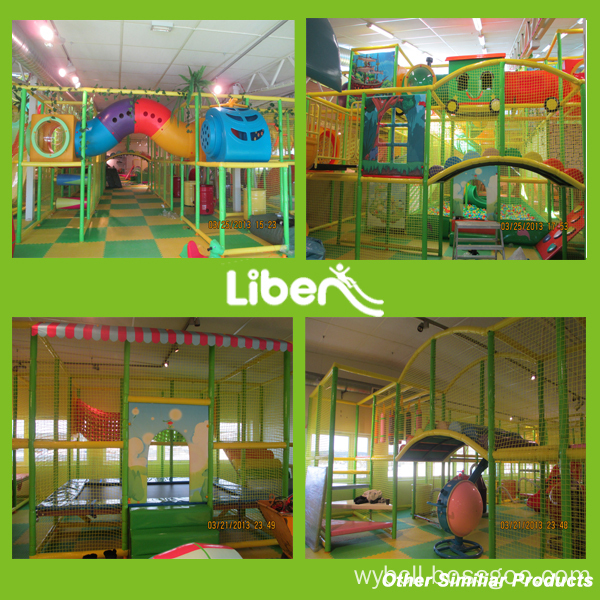
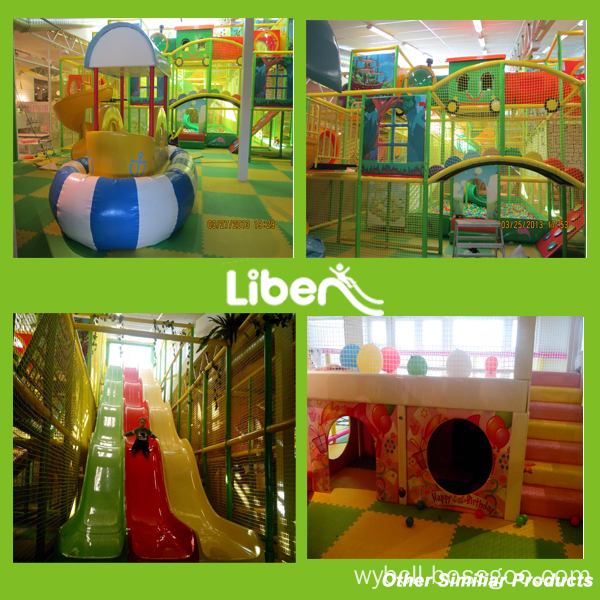
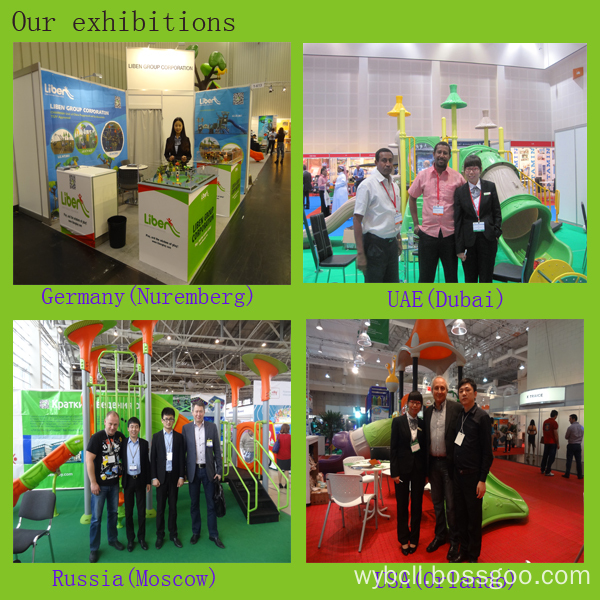
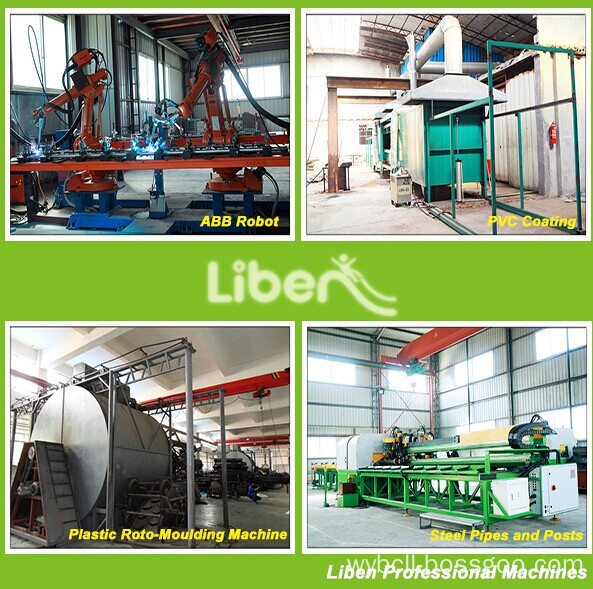
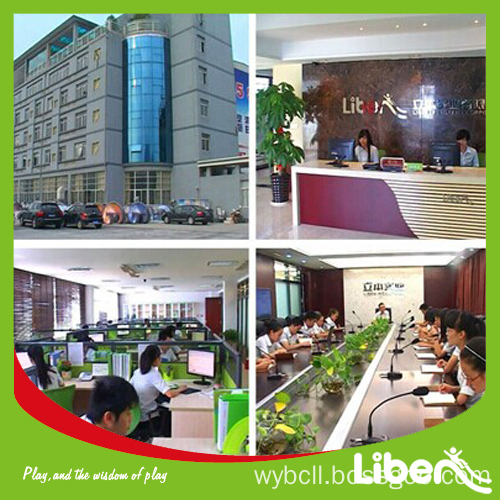
Plastic Rocking Horse, Wooden Rocking Horse, Baby Rocking Horse, Kids Rocking Horse
Liben Group Corporation , https://www.indoortrampoline.de